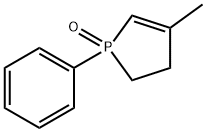
3-Methyl-1-phenyl-2-phospholene 1-oxide synthesis
- Product Name:3-Methyl-1-phenyl-2-phospholene 1-oxide
- CAS Number:707-61-9
- Molecular formula:C11H13OP
- Molecular Weight:192.19
Yield:707-61-9 99.1%
Reaction Conditions:
with 2,6-di-tert-butyl-4-methyl-phenol in chloroform at 65; for 24 h;Inert atmosphere;Sealed tube;Large scale;
Steps:
2 Production of 3-methyl-1-phenyl-2-phospholene oxide (MPPO)
[0046] Example 2 is also a method of producing MPPO in accordance with the instant disclosure. The reactants, solvents, and additives, and amounts thereof used to form the MPPO are set forth in Table 2 below. [0047] To start, a reactor is evacuated, i.e., a vacuum applied, and a vacuum leak check is performed to determine a vacuum loss. The reactor maintains vacuum, with the vacuum loss being less than 5 mm Hg (0.1 psi) over 10 minutes. The vacuum is withdrawn and the reactor is pressurized with nitrogen to 2586 mm hg (50 psi). After the vacuum leak check, a pressure leak check is again performed to determine a pressure loss. The reactor maintains pressure, with the pressure loss being less than 13 mm hg (0.25 psi) over 15 minutes. The reactor is then cooled to a temperature of about 25 °C (77 °F). The halogenated hydrocarbon solvent and the antioxidant are first charged into the reactor and a nitrogen blanket is then applied. The dihalohydrocarbylphosphine is then charged into the reactor and a reactor mix speed is set at about 150 RPM. The reactor is then vented and 2-methyl-l,3-butadiene, having a temperature of about 0°C (32°F), is charged into the reactor. Once the 2- methyl- 1,3 -butadiene is charged into the reactor, the reactor is sealed and the reactor mix speed is set at about 500 RPM. The reactor, cooled to a temperature of about 23 °C (73 °F), is purged with nitrogen. Once purged, the reactor is heated to a temperature of about 65°C (149°F) and the reaction is allowed to progress for about 24 hours to form the adduct. [0048] In contrast to the method of Example 1 , the method of Example 2 includes the step of neutralizing the adduct with a solution of metal hydroxide and water via a hydrolysis reaction. As such, after 24 hours of agitation at about 65 °C (149°F), the reactor is vented and cooled to a temperature of about 25 °C (77 °F). The solution of metal hydroxide and water is gradually charged into the reactor and the reactor ispurged with nitrogen, sealed, and the reactor mix speed is set at 150 RPM. After about 20 hours of mixing, the reactor is vented. Once mixed and vented, excess reactants and solvents are removed/stripped. More specifically, the reactor temperature is gradually increased to about 55°C (131°F) and excess 2-methyl-l,3- butadiene is removed first. The reactor temperature is increased again to about 65°C (149°F) and the chloroform and other reactants, solvents, additives and by-products are removed. [0049] Once the excess volatile reactants and solvents are removed/stripped, the MPPO is extracted from the reactor. [0050] The solution of metal hydroxide and water is a 25% solution of sodium hydroxide and water.
References:
WO2014/164045,2014,A1 Location in patent:Paragraph 0021; 0046; 0047; 0048; 0049, 0050
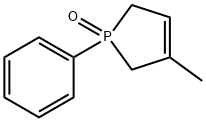
7564-51-4
45 suppliers
inquiry
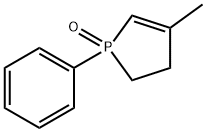
707-61-9
216 suppliers
$17.00/1g

17154-12-0
3 suppliers
inquiry
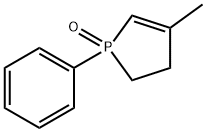
707-61-9
216 suppliers
$17.00/1g
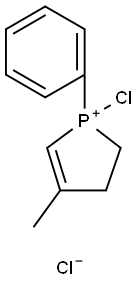
17786-49-1
0 suppliers
inquiry
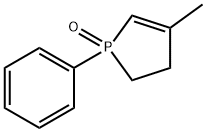
707-61-9
216 suppliers
$17.00/1g
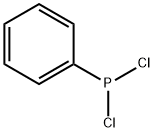
644-97-3
9 suppliers
$14.00/5g
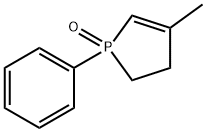
707-61-9
216 suppliers
$17.00/1g