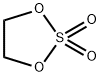
ETHYLENESULFATE synthesis
- Product Name:ETHYLENESULFATE
- CAS Number:1072-53-3
- Molecular formula:C2H4O4S
- Molecular Weight:124.12
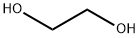
107-21-1
1298 suppliers
$10.00/25g
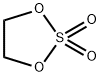
1072-53-3
285 suppliers
$6.00/5g
Yield:1072-53-3 98.03%
Reaction Conditions:
Stage #1: ethylene glycolwith dicyclohexyl-carbodiimide at 5;Flow reactor;Large scale;
Stage #2: with sulfuryl dichloride at 5;Flow reactor;Large scale;Reagent/catalyst;Temperature;
Steps:
1-6; 1-6 Example 1
step 1) At room temperature, 6.2068kg (100mol) of ethylene glycol, 31.034kg of dimethyl carbonate and 0.0310kg of N,N'-dicyclohexylcarbodiimide (the mass ratio of the three is 1: 5: 0.005, ethylene glycol mass percentage of 19.98%), pass into heat exchanger 1 and mix well and pre-cool to 5 ° C to obtain ethylene glycol mixed solution (water content < 50ppm) in addition, a filter (filtered) is installed between heat exchanger 1 and microchannel reactor, the accuracy of the device is 0.1 μm). At the same time, 14.8467kg (110mol) of sulfonyl chloride was passed into heat exchanger 2 and pre-cooled to 5°C; It will be explained that, in this step (1), the ethylene glycol, dimethyl carbonate,N,N'-dicyclohexylcarbondiimide is dissolved at a specified proportion of the flow rate into the heat exchanger 1, the mixing and pre-cooling is completed in a continuous flow, thereby forming a glycol mixture, and then continuously directly into the microchannel reactor, e.g., using a feedback type real-time flow control metering pump and flow meter and set the flow rate of ethylene glycol on average 62.068g/min ( 1.0mol/min), the average flow rate of the ethylene glycol mixture is set to 372.72g/min, and the average flow rate of sulfonyl chloride is set to 148.467g/min (1.1mol/min); Further, the specified proportion of the mass of ethylene glycol, dimethyl carbonate, N,N'-dicyclohexylcarbondiimide, once passed into a large heat exchanger 1 to remove moisture and pre-cooling, thereby forming a glycol mixture, and then fed together in a microchannel reactor; the present invention is preferably at a specified proportion of the flow rate of the above ethylene glycol, dimethyl carbonate, N,N'-dicyclohexylcarbodiimide is continuously passed through in heat exchanger 1, pre-cooled and mixed during continuous flow, and continuously directly into the microchannel reactor. It will be noted that the present invention is a continuous reaction, the amount of ethylene glycol and sulfonyl chloride is not particularly limited, may increase the amount of ethylene glycol and sulfonyl chloride feeding, may also be continuously supplied according to the amount of production plan. In order to well illustrate the reaction process of the present invention and its yield and yield, in Example 1, only the total amount of ethylene glycol fed is 6.2068kg (100mol) and the total amount of the feed is 14.8467kg (110mol) of sulfonyl chloride as an example, only a continuous reaction time of only about 100min is given as an example, embodying the continuous reactivity of the method of the present invention and enhancing the effect of mass transfer and heat transfer, In fact, the continuous reaction of the present invention may be continuously carried out for several minutes or several hours, may also be continuously carried out for a day or a few days or more, is conducive to continuous precision production in the industry. Step (2) According to the molar ratio of ethylene glycol and sulfonyl chloride reaction molar ratio of 1.0:1.1, the ethylene glycol mixture at a flow rate of 372.72g / min (equivalent to the flow rate of ethylene glycol is 62.068g / min, i.e., 1mol / min), the sulfonyl chloride at a flow rate of 148.467g / min (equivalent to the flow rate of sulfonyl chloride is 1.1mol / min), while flowing into the microchannel reactor, mixed in a microchannel reactor at a temperature of 5 °C, After sufficient mass transfer and heat transfer, the reaction is carried out to obtain a mixture of vinyl sulfate. The equivalent diameter of the pipeline of the microchannel reactor is 5mm, the length is 5000mm, the structural characteristics of the pipeline are thorn-shaped pipes, and the material of the pipe is high purity SiC (>99.9%) or Hastelloy C276. To illustrate, in the present embodiment, the internal size of the microchannel reactor is not particularly limited, as long as the expected reaction effect can be achieved, the microchannel reactor of various sizes and various channel structures may be employed, e.g., the equivalent diameter of the channel of the microchannel reactor may be 1.0mm ~ 15.0mm, the channel length of the microchannel reactor may be 50mm ~ 5000mm, the structural characteristics of the channel may be a round pipe, a square pipe, a thorn pipe or a snake-shaped pipeline; Further, the feed in the microchannel reactor flow time (reaction time) is not particularly limited, can be adjusted by using different lengths of pipes, for example, in Example 1 is only about ten seconds, but as long as the expected reaction effect can be achieved, the flow time (reaction time) can be set to 1s ~ 500s, preferably set to 10s ~ 500s, can also be set to a longer time. Step (3) In a continuous flow state, the vinyl sulfate mixture is delivered to the gas-liquid separator, from the bottom of the gas-liquid separator at a speed of 200L / h into the heat exchanger 3 preheating to 35 ° C nitrogen, the nitrogen from the top of the gas-liquid separator runs out, taking away the hydrogen chloride gas in the vinyl sulfate mixture, wherein the water content of the nitrogen is less than 5ppm, after the removal of hydrogen chloride, to obtain a vinyl sulfate solution. Step (4) The vinyl sulfate solution was evaporated and concentrated under anhydrous environment using a concentrated crystal separator, and dried for 30min at a drying temperature of 40 °C and a relative vacuum of -0.0995MPa to give 12.1672 kg (98.03 mol) of vinyl sulfate with a yield of 98.03% (relative to ethylene glycol). Tested by gas chromatography, the purity of vinyl sulfate is 99.97%.
References:
CN114591288,2022,A Location in patent:Paragraph 0066; 0115-0128; 0133-0151
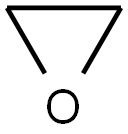
75-21-8
213 suppliers
$39.10/1mL
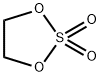
1072-53-3
285 suppliers
$6.00/5g
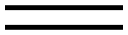
74-85-1
94 suppliers
$79.00/11l
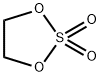
1072-53-3
285 suppliers
$6.00/5g
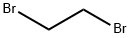
106-93-4
370 suppliers
$15.00/5g
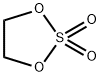
1072-53-3
285 suppliers
$6.00/5g
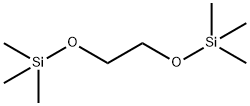
7381-30-8
207 suppliers
$10.00/250mg
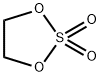
1072-53-3
285 suppliers
$6.00/5g