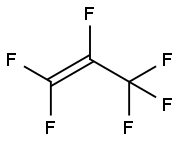
Hexafluoropropylene synthesis
- Product Name:Hexafluoropropylene
- CAS Number:116-15-4
- Molecular formula:C3F6
- Molecular Weight:150.02
3 CF2=CF2 → 2 CF3CF=CF
This reaction is carried out in a closed continuous reactor at 600 to 900°C. The yield can be improved at low partial pressure, achieved either by operating under reduced total pressure (down to 0.1 bar) or by injecting an inert diluent such as steam or CO2.
Significant quantities of by-products, including the highly toxic perfluoroisobutylene (PFIB), are formed during the pyrolysis of TFE. Such by-products are either incinerated directly or are collected and transported for incineration at a remote facility.
Hexafluoropropylene can also be prepared from chlorodifluoromethane, or produced from various chlorofluorocarbons.
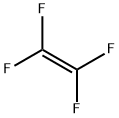
116-14-3
53 suppliers
inquiry
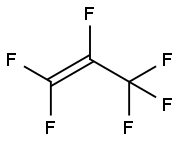
116-15-4
181 suppliers
$40.00/25g
Yield:116-15-4 96.5%
Reaction Conditions:
with silicon carbide at 450 - 850; for 3.33333E-05 h;
Steps:
2
The material of the cracking tube is high nickel alloy tube, the raw material is TFE, the energy storage powder is silicon carbide powder, and the cooling medium is water.Step S1: The tetrafluoroethylene (TFE) gas phase is passed into the mixer;Step S2: Control the preheater temperature at 450 ° C, preheat tetrafluoroethylene (TFE) gas;tep S3: The silicon carbide powder passing through the powder temperature controlled heater is heated to 850 ° C;Step S4: After the preheated TFE high-speed air entrainment has been in the powder temperature control heater to complete the heating of silicon carbide powder together into the cracking tube, in the silicon carbide powder under high temperature cracking reaction to produce hexafluoropropylene; reaction Time control in the 0.12s or so.Step S5: The hexafluoropropene produced in step S4 is passed out from the cracking tube and then enters the cyclone separator. The silicon carbide powder is separated and rapidly cooled to below 450 ° C in the quench. The gas leaving the quench tank enters the subsequent treatment unit through the gas Separation and distillation, to obtain hexafluoropropylene products.The silicon carbide powder separated from the cyclone directly enters the powder temperature controlled heater and is reheated to the desired temperature.That is, silicon carbide powder is circulated in powder temperature controlled heaters, cracking tubes and cyclones.The cooling medium in the chiller is water, and the water after the quench is used to heat the TFE to heat it up to conserve energy.The residual gas separated in the subsequent treatment unit was returned to the mixer and the hexafluoropropene finished product was prepared by the above steps S1-S5 together with tetrafluoroethylene (TFE) at a ratio of 1: 6.Product yield was 96.5%
References:
CN104086341,2016,B Location in patent:Paragraph 0056-0064
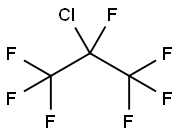
76-18-6
25 suppliers
inquiry
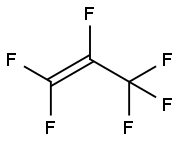
116-15-4
181 suppliers
$40.00/25g

355-49-7
76 suppliers
$29.00/1g
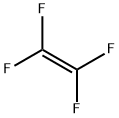
116-14-3
53 suppliers
inquiry
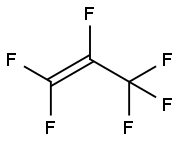
116-15-4
181 suppliers
$40.00/25g
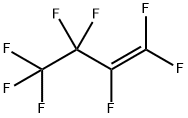
357-26-6
12 suppliers
$195.00/5G
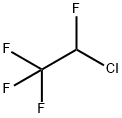
2837-89-0
0 suppliers
inquiry
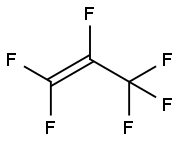
116-15-4
181 suppliers
$40.00/25g