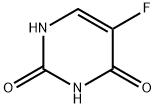
5-Fluorouracil synthesis
- Product Name:5-Fluorouracil
- CAS Number:51-21-8
- Molecular formula:C4H3FN2O2
- Molecular Weight:130.08
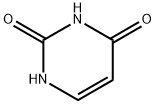
66-22-8
831 suppliers
$5.00/10g
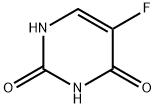
51-21-8
837 suppliers
$5.00/5g
Yield:51-21-8 89.4%
Reaction Conditions:
with fluorine;trifluoroacetic acid at -10; under 2250.23 Torr;Inert atmosphere;Reagent/catalyst;Temperature;Pressure;
Steps:
1
(Figure 1) corning straight channel module 1 (as premix preheat module), corning "heart" microchannel reaction module 6, corning straight channel module 1 (as quenching module) and heat transfer module 8 , And the continuous flow microchannel reaction system is composed according to the reaction flow shown in Fig. The reaction heat transfer medium is made of heat transfer oil. According to the principle of forced heat transfer of microchannel reactor, only two temperature measurement points are set in the inlet and outlet of the reactor. Before the reaction, the microchannel reaction system and the connecting pipeline were treated by dewatering and degreasing respectively. The system and the connecting line were passivated with 5mol% fluorine and nitrogen gas mixture to carry out the airtightness check of 1.0MPa. The uracil solution (i.e., a mixture of uracil and anhydrous hydrofluoric acid, and the concentration of uracil 7%) was continuously added to the microchannel reaction system by the 1-liquid chestnut (Fig. 3). With the gas mass flow meter of Fig. 3, A 20 mol% fluorine-nitrogen mixed gas was continuously added to the microchannel reaction system.Set the heat exchanger temperature 0 ° C, ie the reaction temperature. Set the reaction pressure 0. IMPa. The molar ratio of fluorine gas to uracil was 1.2: 1, and the molar ratio of fluorine gas to uracil was 1.2: 1. The reaction mixture was heated into the "heart-shaped" microchannel reaction module 4 by the microchannel pre-heating module 3 and the fluorine-nitrogen mixed gas was directly introduced into the "heart-shaped" microchannel reaction module 4 through the gas mass flow meter. Heart-shaped "microchannel reaction module 4-9, the fluorine-nitrogen mixture reacts with uracil. The crude reaction product is separated by a gas-liquid separator after quenching the module 10 and then treated by a system and dried to obtain a 5-fluorouracil product. The reaction product was analyzed by liquid chromatography. The results showed that the purity of 5-fluorouracil reached 98.6% and the product yield was 86.7%. The same Corning microchannel reactor was used as in Example 1, and the same connection method and control method were used. This example changes the reaction conditions.Set the heat exchanger temperature -10 ° C, ie the reaction temperature. Set the reaction pressure 0. 3MPa. The reaction material 2 is a uracil solution, i.e., a mixture of uracil and trifluoroacetic acid, with a mass concentration of uracil of 7% and a feed rate of 50 g / min. The raw material 1 is 20 mol% of the fluorine-nitrogen mixed gas, and the feed rate is 4. 2 L / min. The molar ratio of fluorine to uracil is 1. 2: 1. Reaction of raw materials 2 uracil solution through the micro-channel pre-mixed preheating module 3 into the "heart-shaped" micro-channel reaction module 4, fluorine nitrogen mixture through the gas mass flow meter directly into the micro-channel reaction module 4, in the "heart" micro In the channel reaction module 4-9, the fluorine-nitrogen mixture reacts with uracil. The crude reaction product is separated by a gas-liquid separator after quenching the module 10 and then treated by a system and dried to obtain a 5-fluorouracil product. The reaction product was analyzed by liquid chromatography, the purity of 5-fluorouracil reached 99. 2%, the product yield 89. 4%.
References:
CN106432099,2017,A Location in patent:Paragraph 0028-0031; 0057-0061
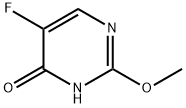
1480-96-2
291 suppliers
$9.00/10g
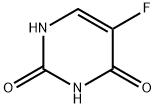
51-21-8
837 suppliers
$5.00/5g
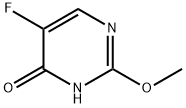
1480-96-2
291 suppliers
$9.00/10g
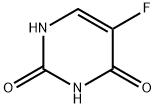
51-21-8
837 suppliers
$5.00/5g
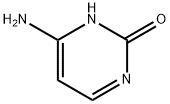
71-30-7
754 suppliers
$5.00/10g
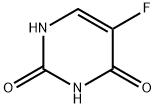
51-21-8
837 suppliers
$5.00/5g
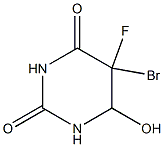
1820-76-4
0 suppliers
inquiry
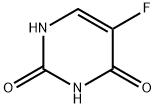
51-21-8
837 suppliers
$5.00/5g