
AMMONIUM CARBAMATE synthesis
- Product Name:AMMONIUM CARBAMATE
- CAS Number:1111-78-0
- Molecular formula:CH6N2O2
- Molecular Weight:78.07
Yield:-
Reaction Conditions:
with ammonia in water at 182; under 116262 Torr; for 0.333333 h;Industry scale;Compressed gas(es);
Steps:
1
Table 1 shows the material balance, temperatures and pressures at a rating, i.e., at a plant load of 100% in an example of production of 1725 t/day of urea when the apparatus for synthesizing urea of the embodiment shown in FIG. 1 is used. In Table 1, ammonium carbamate is shown as ammonia and carbon dioxide. Out of the raw material ammonia 1 at a pressure of 23 MPaG and a temperature of 30° C., 39.7 t/h were heated by the heat exchanger G to 140° C. and then supplied to the ejector E via the line 1a and 1.0 t/h was supplied to the condenser B via the line 1b. On the other hand, carbon dioxide 2 at a pressure of 0.1 MPaG and a temperature of 40° C. was pressurized by a compressor (not shown in the figure) and carbon dioxide at a pressure of 16 MPaG and a temperature of 120° C. was obtained. And 41.2 t/h of this carbon dioxide were supplied to the stripper C through the line 2a and 9.1 t/h were supplied to the synthesis reactor A through the line 2b to produce urea. The supplied ammonia 1a was mixed in the ejector E with the synthesis solution 6 at a pressure of 15.2 MPaG from the condenser B, and supplied at a pressure of 15.5 MPaG from the line 8 to the synthesis reactor A. The synthesis reactor A was operated at a pressure of 15.5 MPaG, at a temperature of 182° C., at N/C of 3.7, at H/C of 0.58 and for a residence time of 20 minutes, and urea was synthesized. The conversion ratio based on carbon dioxide in the synthesis reactor was 63%. The synthesis solution 4 containing urea from the upper part of the synthesis reactor A was supplied to the stripper C. Medium-pressure steam 15 was supplied to the shell side of the stripper C to supply heat for the decomposition of carbamate and went out as condensed water 16. On the tube side of the stripper C, the decomposition of carbamate and stripping were performed at an upper part temperature of 184° C., at a lower part temperature of 171° C., and at a pressure of 15.5 MPaG, and gaseous components were separated in the upper part. The gaseous components 5 were fed to the condenser B, and the synthesis solution 10 which had left the bottom of the stripper C was fed to the decomposition apparatus. Then, 134.6 t/h of the gaseous components from the stripper C (in the line 5) and 62.2 t/h of the recycled carbamate liquid (in the line 11) were fed to the condenser B. The condenser B was operated at a temperature of 180° C., at a pressure of 15.2 MPaG, at N/C of 2.9, at H/C of 0.65, and for a residence time of 20 minutes, and urea and the like were synthesized. The conversion ratio based on carbon dioxide in the condenser was 46%. The density of the condensed liquid was measured by use of a radiation type density meter I (made by Ohmart Corporation, trade name: DENSART D-3000) installed in the line 6. The density of the condensed liquid was 1025 kg/m3. The temperature of the condensed liquid during the density measurement was 180° C. Other operating conditions are shown in Table 1. From the liquid amount of the recycled carbamate and the simplified formula of a plant load, the H/C of the condensed liquid 6 was estimated at 0.65. The flow rate of the fluid at the outlet of the condenser was calculated. As a result, the flow rate of the ammonia component was 91.1 t/h, the flow rate of the carbon dioxide component was 81.2 t/h, and the flow rate of the water component was 21.5 t/h. In this calculation, it was assumed that the flow rate of the carbon dioxide component is the same as that in the material balance at a 100% load. A calculation to raise the N/C of the fluid at the outlet of the condenser to 3.0 was performed. An ammonia component in an amount of (81.2/44)×3.0×17=94.1 (t/h) is necessary. Therefore, it is only necessary that the amount of ammonia be increased by 94.1-91.1=3.0 t/h. The amount of the raw material ammonia was increased from 40.7 t/h to 43.7 t/h, with the result that in 40 minutes, the N/C in the condenser rose to 3.0. As a result, the N/C in the synthesis reactor was able to be raised from 3.7 to 3.8. A process and an apparatus for synthesizing urea of the present invention can each be favorably used in a process and an apparatus for synthesizing urea which manufacture urea from ammonia and carbon dioxide.
References:
US2006/270872,2006,A1 Location in patent:Page/Page column 4; 10-11
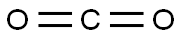
124-38-9
134 suppliers
$214.00/14L

1111-78-0
193 suppliers
$10.00/5g
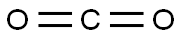
124-38-9
134 suppliers
$214.00/14L
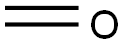
50-00-0
897 suppliers
$10.00/25g
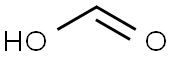
64-18-6
1130 suppliers
$22.12/250ML
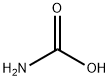
463-77-4
7 suppliers
inquiry

1111-78-0
193 suppliers
$10.00/5g
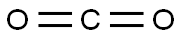
124-38-9
134 suppliers
$214.00/14L
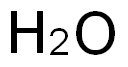
7732-18-5
498 suppliers
$13.50/100ML

1111-78-0
193 suppliers
$10.00/5g
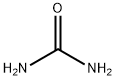
57-13-6
784 suppliers
$5.00/5g
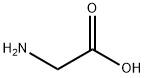
56-40-6
1327 suppliers
$5.00/25g

1111-78-0
193 suppliers
$10.00/5g