
Diethylene glycol synthesis
- Product Name:Diethylene glycol
- CAS Number:111-46-6
- Molecular formula:C4H10O3
- Molecular Weight:106.12
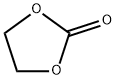
96-49-1
531 suppliers
$6.00/100g
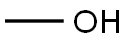
67-56-1
788 suppliers
$9.00/25ml
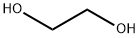
107-21-1
1370 suppliers
$10.00/25g
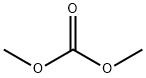
616-38-6
719 suppliers
$5.00/5G

111-46-6
1104 suppliers
$5.00/25g
Yield:616-38-6 91.3% ,107-21-1 91.3%
Reaction Conditions:
sodium hydroxide at 49.8 - 56.2; under 342.034 Torr;Product distribution / selectivity;Industry scale;
Steps:
3, 7 EXAMPLE 3
Dimethyl carbonate (DMC) and ethylene glycol (EG) were continuously produced from ethylene carbonate (EC) and methanol (MeOH) by using substantially the same production system as in Example 1, except that continuous multi-stage distillation column 1 had an inner diameter of 5.36 cm (cross-sectional area: 0.00225 m2) and a packing height of 100 cm. The operation for the production of DMC and EG was performed in substantially the same manner as in Example 1, except that the reaction conditions we re as follows: EC was fed at a flow rate of 612.2 g/h; a 4.8% by weight solution of sodium hydroxide (as a catalyst)(instead of potassium hydroxide) in ethylene glycol was fed at a flow rate of 25.4 g/h (instead of 32.6 g/h); a mixture of MeOH and DMC was fed through conduit 5 at a flow rate of 1,737 g/h; the reaction temperature of column bottom 8 was 56.2° C.; and gas density ρg and gas velocity ug in distillation column 1 were 0.545 kg/of and 0.393 m/s, respectively, and hence the F-factor of distillationo column 1 was 0.29. A column top condensate from column 1 (containing MeOH and DMC in concentrations of 67.2% by weight and 32.8% by weight, respectively) was obtained at a flow rate of 1,902 g/h. A liquid reaction mixture (containing MEOH, DMC, EG and EC in concentrations of 45.7% by weight, 1.2% by weight, 47.1% by weight and 6.0% by weight, respectively) was withdrawn from column bottom 8 of distillation column 1 at a flow rate of 888.7 g/h and, as in Example 1, fed to low boiling point mixture-recovering column 10 which was operated under the same conditions as in Example 1. A part of a column top condensate from column 10 (low boiling point mixture-recovering column) was returned in a liquid form to column bottom 8 of distillation column 1 at a flow rate of 416 g/h. A part of a liquid withdrawn from column bottom 16 of column 10 was recovered from the production system through conduit 20 at a flow rate of 472.7 g/h. The withdrawn liquid (bottom liquid of column 10) contained EG, EC and by-produced diethylene glycol (DEG) in concentrations of 88.5% by weight, 11.3% by weight and 0.02% by weight, respectively. In the withdrawn liquid, 2-methoxyethanol (2ME) (as a possible by-product) was not detected. From the above data, it can be seen that the conversion of EC was 91.3%, the yield of DMC was 91.3% (DMC was produced at a production rate of 572 g/h), the selectivity for DMC was not lower than 99.9%, the yield of EG was 91.3% (EG was produced at a production rate of 394 g/h), and the selectivity for EG was not lower than 99.9%. Also, the volume (V) of the reaction zone in continuous multi-stage distillation column 1 was calculated as follows: V=?×2.682×100/1,000=2.26 liter. Therefore, the productivity of DMC in terms of the space time yield was: 572/2.26=253 g/liter·h. The conditions and results of the trans-esterification reaction are shown in Table 1.
References:
US6346638,2002,B1 Location in patent:Page column 25-32
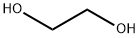
107-21-1
1370 suppliers
$10.00/25g
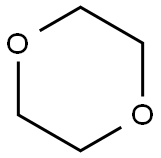
123-91-1
708 suppliers
$17.00/25g

111-46-6
1104 suppliers
$5.00/25g
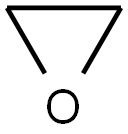
75-21-8
239 suppliers
$39.10/1mL

111-46-6
1104 suppliers
$5.00/25g

112-27-6
778 suppliers
$6.00/100g
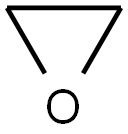
75-21-8
239 suppliers
$39.10/1mL
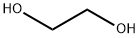
107-21-1
1370 suppliers
$10.00/25g

111-46-6
1104 suppliers
$5.00/25g
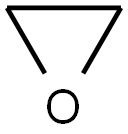
75-21-8
239 suppliers
$39.10/1mL
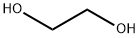
107-21-1
1370 suppliers
$10.00/25g

111-46-6
1104 suppliers
$5.00/25g

112-27-6
778 suppliers
$6.00/100g