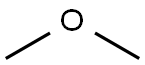
Dimethyl ether synthesis
- Product Name:Dimethyl ether
- CAS Number:115-10-6
- Molecular formula:C2H6O
- Molecular Weight:46.07
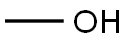
67-56-1
782 suppliers
$9.00/25ml
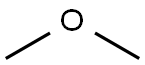
115-10-6
106 suppliers
$75.00/25g
Yield:115-10-6 99%
Reaction Conditions:
NaPZSM-5 in water at 250; under 7600.51 Torr;Product distribution / selectivity;
Steps:
1; 2; 3
Example 1; 300 liters of an NaPZSM-5 catalyst was loaded into a fixed-bed reactor. In this state, the catalyst was pre-treated at 400°C for 1 hour while nitrogen was supplied at a flow rate of 18.5 NmVmin, after which the temperature of the reactor was set to 250°C. Subsequently,
References:
WO2008/26887,2008,A1 Location in patent:Page/Page column 10-13
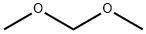
109-87-5
377 suppliers
$9.00/5g
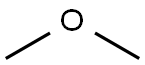
115-10-6
106 suppliers
$75.00/25g
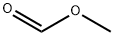
107-31-3
355 suppliers
$16.00/25mL
201230-82-2
1 suppliers
inquiry
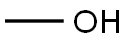
67-56-1
782 suppliers
$9.00/25ml
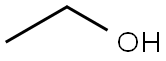
64-17-5
758 suppliers
$10.00/50g
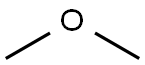
115-10-6
106 suppliers
$75.00/25g
201230-82-2
1 suppliers
inquiry
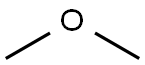
115-10-6
106 suppliers
$75.00/25g
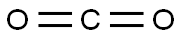
124-38-9
133 suppliers
$214.00/14L
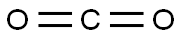
124-38-9
133 suppliers
$214.00/14L
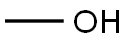
67-56-1
782 suppliers
$9.00/25ml

34557-54-5
0 suppliers
inquiry
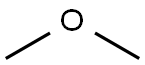
115-10-6
106 suppliers
$75.00/25g
201230-82-2
1 suppliers
inquiry