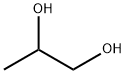
Propylene glycol synthesis
- Product Name:Propylene glycol
- CAS Number:57-55-6
- Molecular formula:C3H8O2
- Molecular Weight:76.09
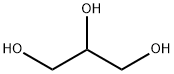
56-81-5
1723 suppliers
$5.00/25g
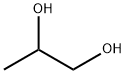
57-55-6
1618 suppliers
$5.00/1g
Yield:57-55-6 99%
Reaction Conditions:
with sulfuric acid;hydrogen;Ni/Re pH=6.9 - 12.1;Industry scale;
Steps:
3
An unrefined propylene glycol product was made by the hydrogenolysis of a biobased giycero) over a Ni/Re catalyst. Approximately 5200 kg of reactor product were neutralized over 19 batches. The average sulfuric acid dosage was 0.33 gl 100g of feed. There were two batches where the sulfuric acid loading was significantly less (0.03g/ 00g). The cause was undetermined, but may have been due to low concentration of propylene glycol due to start-up or shut down of the reactor. The average pH of the reactor product was 12.1 and the average neutralized pH was 6.9.[0046] The thus-neutralized product was then distilled according to the embodiment shown in Figure 2, beginning with an alcohol removal step. This column was run under atmospheric pressure. Due to equipment constraints a high reflux ratio was used. This resulted in less water overhead (4-12 wt %) than indicated by process modeling (27 wt %). The propylene glycol yield was >99%. The other parameters are given in the table below. Table 1 : Alcohol Removal summar[0047] The next step was a primary water removal step, designed to remove substantially all of the water so that the bottoms to a subsequent glycerol removal step would contain less than 1 wt % of water. This step was completed successfully. The water concentration was brought down to 0.6%. The propylene glycol yield was >99%. There were several operational problems due to salts in the reboiler and feed lines, but these were mainly believed to be due to not having the correct steam flow or other operational issues. There was no evidence of solids formation in the packing, which had been a concern with the low levels of water targeted. The salts would wash out easily with water, and the column was continuously run for approximately 5 days without having problems with the solids. The results are given in the table below. Table 2: Water Removal Column (WRC) Performance[0048] The next separation was to remove the residual unreacted glycerol in a glycerol removal step. This step went very smoothly with no significant problems. The yield was >99% with 0.5% glycerol in the distillate. Other conditions and results were as reported in Table 3: Table 3: Glycerol Removal Column (GRC) Performance[0049] Ethylene glycol was next to be separated out as a principal component of the PG product mixture. The results were not as good as hoped, unfortunately, primarily due to operational error. The goal was to maximize yield and the distillate that went forward was not within specification (600 ppm on a propylene glycol basis). There was also one upset that caused ethylene glycol at 1.2% to go forward. Propylene glycol yield was between 95 and 98%, and the bulk product forward for the subsequent butanediol removal step had 5700 ppm ethylene glycol and 200 ppm 1 ,2-butanediol, as compared to the 500 ppm ethylene glycol and 50 ppm 1 ,2-butanediol expected from modeling. During the run, the ethylene glycol concentration was brought to approximately 45%, indicating that the amount of ethylene glycol in the feed has an effect on the propylene glycol yield. This column was run at 15.6 in Hg absolute pressure. The results are given in the table below. Table 4: Ethylene Glycol Removal Column (EGRC) Performance*One run was as low as 540ppm[0050] The final distillation step undertaken was for the removal of 2,3- butanediol (and 2,3-pentanediol and other lighter impurities). The goal of this step was to take USP grade propylene glycol as a bottoms product with less than 1000 ppm total butanediols and pentanediols. This specification was met, even with the additional ,2-butanediol from errors in the previous step. The yield was 95-97%. The column was run at 10.7 in Hg absolute pressure. The final product had no detectable epoxides (0.2 ppm LOD). The results are summarized in the table below. The APHA color of the samples of the bottoms product was 3 and the specification was 10. A sample of the final propylene glycol product was given to a sensory group and found to be satisfactory. 5Table 5: Butanediol Removal Column (BRC) Performance*Reflux ratio will vary greatly due to the relatively low distillate rate**200 ppm was 1 ,2-BDO which is normally removed with EG, however an upset sent some forward
References:
WO2012/125276,2012,A2 Location in patent:Page/Page column 16-21
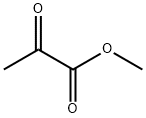
600-22-6
387 suppliers
$6.00/5g
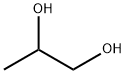
57-55-6
1618 suppliers
$5.00/1g
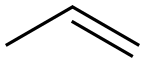
187737-37-7
1 suppliers
inquiry
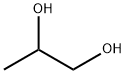
57-55-6
1618 suppliers
$5.00/1g